Reasons an Epoxy Floor Fails and How You Can Avoid It
- Chris Simpson
- Nov 27, 2024
- 4 min read

Many spaces use epoxy flooring thanks to its durability, aesthetic appeal, and ease of maintenance. Yet for all its benefits, this flooring solution is not without potential pitfalls. Explore the common reasons epoxy floors fail and how to avoid repeating the same mistakes with these practical solutions.
Understanding Epoxy Flooring
Epoxy flooring is a resin that hardens into a robust finish when applied to concrete floors. It consists of two main components, resin and hardener, which form a chemical bond that provides the surface with strength and durability.
This type of flooring is common in industrial settings, garages, and commercial properties since it handles heavy loads and resists damage from chemicals and stains. Epoxy has various chemical properties that create a hard, smooth, and visually appealing surface that lasts for years when properly installed.
Improper Surface Preparation
Surface preparation is the first critical step when applying epoxy flooring, yet failing to clean the surface is a common mistake. Skipping or omitting this step results in poor adhesion. The epoxy may not bond correctly to floors coated in grease, oil, and dirt, leading to peeling and cracking.
Additionally, an uneven surface causes the epoxy to pool in certain areas, creating a nonuniform finish. Thoroughly sweep and vacuum the area, then use a degreaser to remove stubborn stains or residues. Grinding or shotblasting the surface creates the necessary texture for optimal adhesion.
Incorrect Mixing Ratios
The effectiveness of epoxy flooring relies on the mixing ratio of resin and hardeners. Precision in mixing helps the materials bond together correctly, providing the strength and durability that epoxy is known for. Eyeballing measurements or failing to mix the components thoroughly results in a weak or sticky finish.
Avoid these issues by using precise measuring tools, such as graduated containers, and follow the manufacturer’s instructions meticulously. Consistent, slow stirring prevents the introduction of air bubbles, which compromise the integrity of the finish.
Environmental Factors
Epoxy curing requires the correct temperature and humidity. High temperatures cause the epoxy to cure too quickly, while low temperatures slow the process, leading to incomplete curing.
Humidity also affects curing; excessive moisture in the air introduces water into the epoxy, leading to clouding or blushing. Investing in a thermometer and hygrometer monitors conditions, ensuring the best environment for applying epoxy flooring.

Poor Application Techniques
The technique used to apply epoxy flooring impacts the outcome. Some of the reasons epoxy flooring fails is due to uneven spreading, incorrect timing, and applying too thin or thick a coat. For a smooth, even finish, start at the back of the room and work your way toward the exit, using a roller to evenly spread the epoxy across the surface.
Timing is important; applying additional layers before the previous layer has cured can result in an uneven finish. Applying the epoxy in thin, even layers is recommended, allowing each to cure before applying the next.
Inadequate Curing Time
Curing time is critical in achieving a durable epoxy floor. Disturbing the epoxy before it fully cures leads to surface issues such as bubbling, peeling, or a tacky finish. Depending on environmental conditions, the curing process takes anywhere from 24 to 72 hours.
Keep foot traffic to a minimum until the epoxy fully cures. Verify the surface’s readiness by gently pressing your fingertips on a hidden area of the floor; if it feels dry and firm, the floor is likely cured. Always refer to the manufacturer’s guidelines for specific curing times and conditions.
Substandard Products
Using low-quality epoxy products leads to disappointing results. Inferior products lack the same durability, color retention, and resistance to chemicals and abrasions as their high-quality counterparts. Quality indicators include high solids content, a clear application guide, and certification from recognized industry standards. Investing in a reputable product will pay off in the long run, providing a floor that stands up to wear and tear.
Moisture Issues
Moisture is one of the leading causes of epoxy floor failure. If the substrate contains too much moisture, it interferes with the bonding process, leading to blisters or bubbles in the finish. Test for moisture content before applying epoxy.
A moisture meter will check the levels in the concrete; if they exceed the recommended threshold, consider using a moisture barrier primer to seal the surface before applying the epoxy. Properly addressing moisture issues will create a strong bond and flawless finish.
Chemical Spills and Stains
Epoxy floors, while resistant to many chemicals, are not impervious to all damage. Harsh chemical spills stain or degrade the surface if not promptly addressed. Consider applying a protective topcoat that adds extra defense against spills and stains. Regularly inspect your floor for chemical damage and address issues promptly to maintain the integrity of the surface.
Surface Abrasion and Damage
Frequent use of heavy machinery causes surface abrasion and damage to epoxy floors. While epoxy is known for its durability, taking measures to minimize wear and tear extends the life of your floor. Use floor mats or protective pads under heavy equipment to reduce direct contact with the surface.
Clean the floors to remove abrasive dirt and debris. Use a topcoat with enhanced abrasion resistance for areas with high traffic to provide additional protection.
Improper Maintenance Practices
Like any surface, epoxy floors require certain maintenance practices to keep them in the best shape. Use a soft-bristle broom or vacuum to remove debris, and mop the floor with a mild detergent and warm water. Avoid cleaners with acidic or abrasive properties. Regular cleaning will keep your floor looking new and prolong its lifespan.
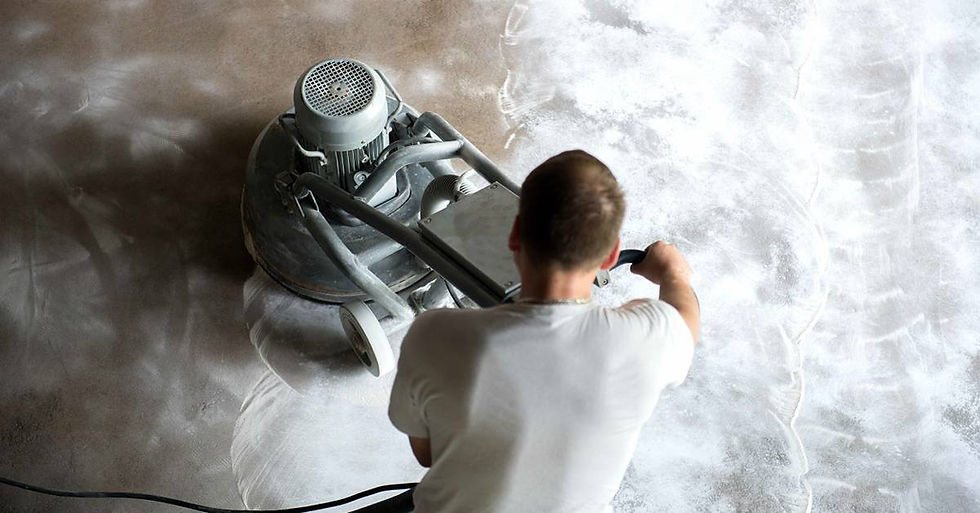
Failure To Address Substrate Issues
If not addressed before application, substrate issues such as cracks, holes, or uneven surfaces lead to epoxy floor failure. These issues create weak points in the epoxy, leading to cracking or peeling.
Thoroughly inspect the substrate and repair damage before applying epoxy. Fill cracks and holes with a suitable filler, then sand the surface to create an even base. Addressing these issues beforehand will create a solid foundation for the epoxy, resulting in a longer-lasting finish.
Achieving a successful epoxy floor installation requires attention to detail at every step of the process. Understanding the common reasons for epoxy floor failure and implementing the solutions provided ensures a long-lasting, durable finish.
If you’re in search of commercial epoxy flooring near you, contact 603 Epoxy for quality application. Our experienced professionals provide the best results and know how to avoid application mistakes for an excellent finish.
Comments